During this incredibly productive weekend in October, a group of dedicated members came together to work on numerous projects, repairs and improvements. A list of projects including an EMAS cistern and a new electrical system for the Kiwanda was prepared beforehand as to allow the work to start more smoothly. It wouldn’t be long until the sound of digging music filled the field as members got out shovels and spades and got to work.
Cistern
During the working weekend we started constructing an EMAS cistern. The EMAS cistern is an alternative for an above ground water storage, which uses very few materials. As we have quite sandy soil we planned to make the sand variation of the emas cistern in which you don’t make a bottleneck but have straight walls. This due to collapsing hazards of the sand based bottleneck while constructing.
After a morning of digging we had a hole with a diameter of 150cm and a depth of about 230cm. The floor of the cistern has a slight slope with the lowest point at the center. This means that all the water can be removed for cleaning purposes. We then started making the reducerring, which is made out of cement and rebar and plastered the inside of the hole with a layer of cement. The next day we added another layer of cement after which we started painting on a pure mixture of just cement and water to seal the cistern and prevent it from leaking. We also added a layer of bricks on top of the cistern walls to place the reducerring onto. In the weeks hereafter we added another layer of bricks on top of the existing layer and plastered the in and outside of the ring. We then placed the reducerring on top. We are currently working on the first flush system and the appropriate connection to the gutter.
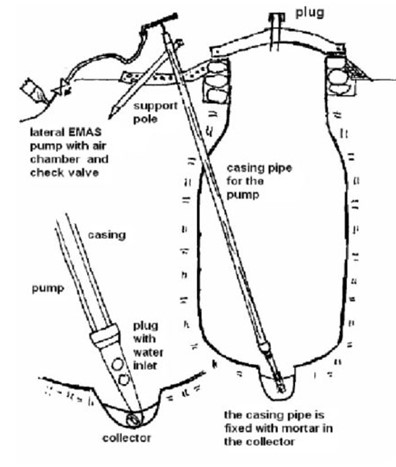
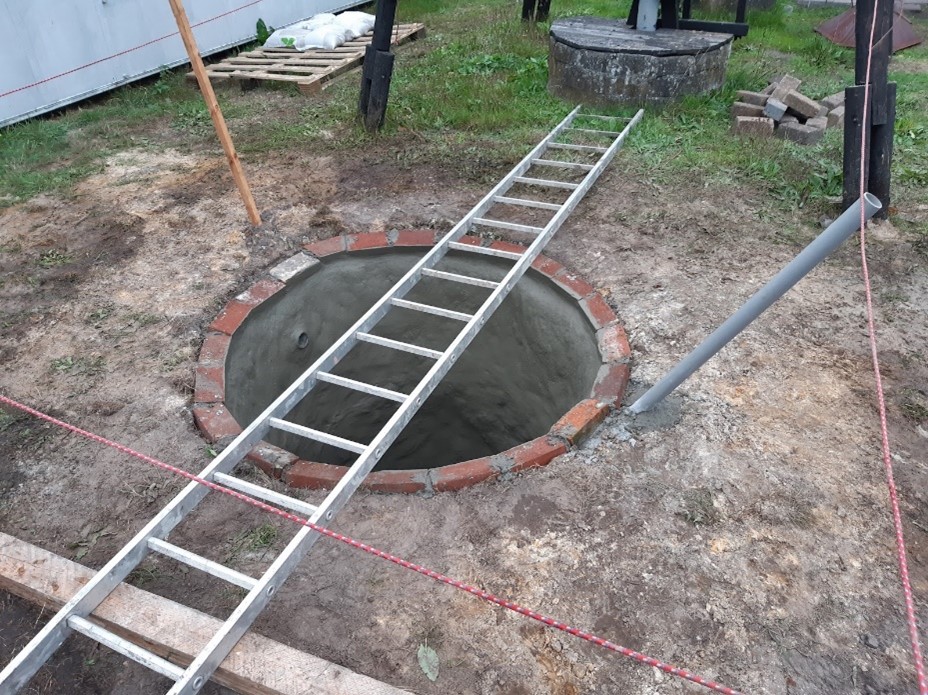
Burgert pump
On Saturday morning we started working on installing a new Burgert pump for testing under the PTB. To do this we first needed to move the pump mount under the flywheel which will power the pump during the testing phase. The last time this had to move, a sledge hammer was used to get the desired result. This was problematic, as there was no room to manoeuvre the sledgehammer to knock the pump mount back. To overcome this issue we lifted the hole assembly from the bottom and used al our strength to push it back to the original spot. After it was secured to the frame we started to measure the distance from the current end of the shaft to the water level to determine the length of tube necessary to mount the pump flush with the water and add a pressure gauge. We also needed to extend the connecting rod from the flywheel to the pump. After some adjusting the pump worked and stopped hitting the valve on the bottom of the pump which would have critically damaged it if turned on without adjustment. On Sunday the only thing that needed work for this project was the sensor electronics which keep track of the performance of the pump. This wasn’t finished at the end of the day however, due to some unforeseen issues with the code that runs the microcontroller.
Electrical system
Besides all these projects a start is made on a new electrical system suspended overhead through the middle of the workshop, bringing power to the moveable workbenches. With this project finished the hassle of extension cords and wire mazes will become a thing of the past in our beloved Kiwanda!
Tags: EMAS, Low cost, water supply